Concrete analysis and elimination method of bad demoulding of injection molding machine If injection molding machine Poor demoulding, also known as die sticking runner, is because the contact surface between the needle mouth and the nozzle arc is not good, the gate material does not demould with the product, and the packaging is abnormal. Generally, the diameter of the main channel shall be large enough to make the gate material not fully solidified when manufacturing demoulding.
Poor demoulding is an important killer of plastic injection molding, whether it is the flow channel of the mold sticking or the product sticking to the mold hole. The root cause of poor demoulding may be different parts of injection molding equipment, or improper injection molding process. Although there is no burr caused by part design and die design error, lack of drawing die slope, drawing die slope and other reasons, sometimes formed parts will appear demoulding phenomenon. When forced to eject, it often forms warped parts, which turn white or crack after ejecting. In particular, the formed parts are stuck on one side of the static mold, and sometimes cannot be ejected.
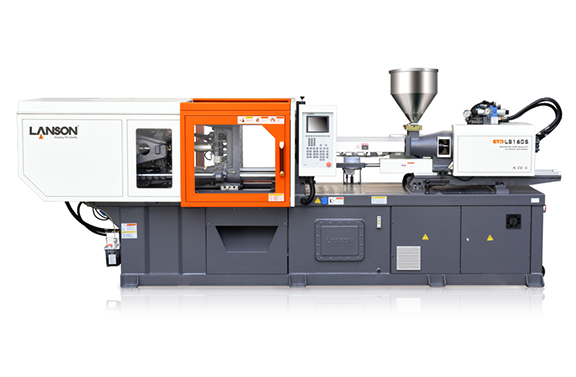
If there are chisel lines, scratches, scars, depressions and other external defects in the mold cavity and runner, the plastic parts will simply attach to the mold, causing difficulty in demoulding. Therefore, the surface finish of mold cavity and runner should be improved as much as possible, and the surface of mold cavity should be chrome plated as much as possible. During polishing, the action direction of the polishing object shall be consistent with the direction of the mold filling molten material.
When the molten material falls off in the scratched part of the mold or the gap between the inserts, demoulding will also cause difficulties. Therefore, the damaged part should be repaired to reduce the insert clearance.
If the mold is not opened at the beginning of injection, it means that the mold will be deformed due to lack of rigidity under the effect of injection pressure. If the deformation exceeds a certain elasticity, the mold cannot be restored to its original state and cannot be used any more. Even if the deformation does not exceed the elasticity of the mold to a certain extent, the molten material is cooled and solidified in a very high state in the mold cavity. After the injection pressure is removed, the mold returns to deformation, and the plastic parts are clamped by the rebound force.