Plastic injection molding machine It is an important manufacturing equipment used to produce various plastic products. However, during its operation, it often encounters some common problems and failures, which may affect production efficiency and product quality. The following are some common problems and failures, as well as possible solutions.
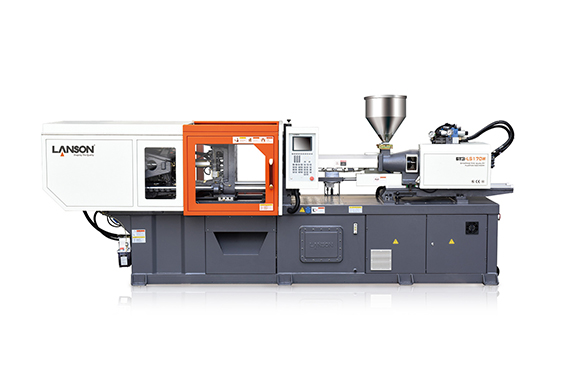
1. Uneven melting: In the injection molding process, sometimes the molten plastic will be uneven, resulting in product defects or deformation. This may be caused by uneven temperature of the heating drum, inconsistent particle size of the plastic, or failure of the conveying system. Solutions include checking the temperature control of the heating drum, adjusting the conveying system to ensure uniform feeding, or using better quality plastic particles.
2. Mold blockage: mold blockage refers to that molten plastic cannot be fully injected into the mold during injection molding, resulting in incomplete product filling or cavity. Possible causes include unreasonable mold design, nozzle blockage or plastic accumulation in the heating cylinder. The solution can be to optimize the mold design, regularly clean the nozzle and heating cylinder, or adjust the injection parameters to improve the plastic fluidity.
3. Temperature control: temperature is a key control parameter in the injection molding process. If the temperature control is inaccurate or unstable, it may lead to poor plastic melting, product size changes or unstable quality. Solutions include calibrating the temperature sensor, cleaning the surface of the heating drum to ensure good heat transfer, or checking the control system to ensure temperature stability.
4. Injection speed: injection speed refers to the speed at which molten plastic enters the mold. If the injection speed is too fast or too slow, it may cause product surface defects, uneven filling or bubbles. The solution can be to adjust the injection speed, optimize the mold runner design, or increase the pressure to improve the plastic filling performance.
5. Improper lubrication and maintenance: the lubrication and maintenance of plastic injection molding machines are critical to their normal operation. Insufficient lubrication or improper maintenance may cause wear, leakage or failure of components. The solution includes regular lubrication of mechanical parts, inspection of seals and pipes to prevent leakage, and regular maintenance according to the manufacturer's recommendations.
Injection molding machine manufacturer Remind you that when facing these problems and failures, it is important to take timely measures to solve them to ensure the normal operation and production quality of the injection molding machine. In addition, regular training of operators and maintenance personnel to improve their skills and knowledge on the operation and maintenance of injection molding machines is also the key to preventing and solving problems. Through reasonable maintenance and effective troubleshooting, the plastic injection molding machine will be able to continuously and stably produce high-quality plastic products.