stay High speed injection molding machine The design and performance of cooling system is very important to realize continuous high-speed production. The function of the cooling system is to rapidly cool and solidify the molten plastic during the injection molding process, so as to release the mold and continue production faster. The following are the key elements for the cooling system of high-speed injection molding machine to ensure continuous high-speed production:
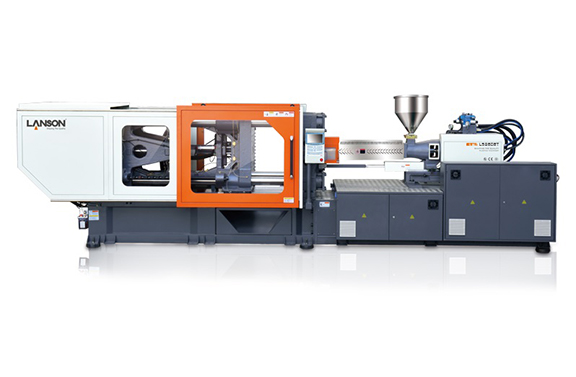
1. Efficient cooling channel design: the cooling channel is the core part of the cooling system, which directly affects the cooling effect and production efficiency. The cooling channel of high-speed injection molding machine shall be designed with reasonable structure and layout to ensure that the cooling medium can fully contact and cover the surface of the injection molding parts, so as to achieve rapid and uniform cooling. The optimized cooling channel design can improve the cooling efficiency and reduce the cooling time, thus realizing continuous high-speed production.
2. Efficient cooling medium: the selection of cooling medium is crucial to the effect of the cooling system. The cooling system of high-speed injection molding machine usually uses water as the cooling medium, because water has good heat conduction performance. At the same time, the use of coolant can further improve the cooling effect. The cooling medium shall have sufficient flow and pressure to ensure a fast and uniform cooling process. By optimizing the supply and circulation system of cooling medium, the cooling effect of continuous high-speed production can be guaranteed.
3. Intelligent cooling control: the cooling system of high-speed injection molding machine is usually equipped with intelligent cooling control system, which can adjust the cooling temperature and cooling time according to the actual production demand. The intelligent cooling control system can monitor the temperature and cooling status of injection molded parts in real time, and automatically adjust the cooling conditions according to the set parameters to ensure the optimal balance between cooling effect and production efficiency. Through precise cooling control, continuous high speed production can be realized and the problem of over cooling or insufficient cooling can be avoided.
4. Maintenance and cleaning of cooling system: keeping the cooling system in good operating condition is very important for continuous high-speed production. Regularly check and clean the cooling channels, coolers and cooling equipment in the cooling system to ensure smooth cooling channels and efficient cooling effect. Replace the cooling medium and coolant regularly to maintain their performance and stability. At the same time, timely repair the water leakage, blockage, damage and other problems in the cooling system to ensure the normal operation of the cooling system.
Lian Sheng Plastic injection molding machine In conclusion, the cooling system of high-speed injection molding machine plays an important role in continuous high-speed production. Through reasonable cooling channel design, efficient cooling medium, intelligent cooling control, and regular maintenance and cleaning, the efficient operation of the cooling system can be ensured to meet the requirements of continuous high-speed production. Therefore, when selecting and using high-speed injection molding machines, the design and performance of the cooling system is one of the important factors that need attention.