How many customized control modes are there for the hydraulic system of the injection molding machine? injection molding machine As a kind of plastic molding processing and production equipment, in order to meet the requirements of the market for injection molded products, it is gradually developing towards the direction of precision, lightweight and miniaturization. The traditional control system has gradually failed to meet the actual production needs. In order to achieve multi-level and micro control of process parameters in the process of precision product molding, it is also necessary to study the accuracy and stability of the control system of the injection molding machine, and strive to improve the production efficiency while ensuring the quality of injection molding products.
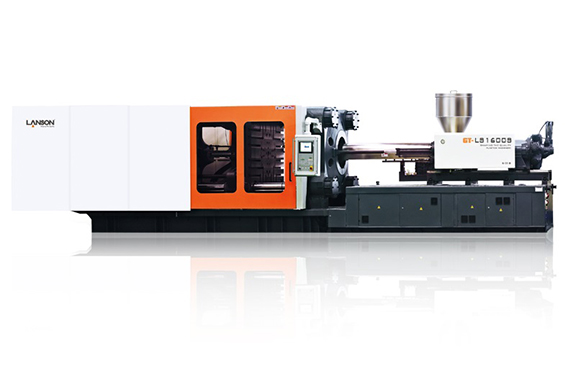
The two main parameters of injection molding machine hydraulic system, pressure and flow, have strong coupling and nonlinear characteristics. Based on the analysis of injection molding process characteristics, in order to better adapt to the production parameters of different injection molding products, the injection pressure and injection speed must be accurately controlled to avoid premature or delayed injection molding downtime. There are quality problems such as full material or polymer overflow. Based on this, it can be judged that it is impossible to adjust by overshoot. It is necessary to select a scientific and feasible control strategy according to the feature that the hydraulic system of the injection molding machine does not allow overshoot, so as to achieve precision control requirements.
For the traditional PID algorithm, its control effect on the pressure and flow parameters of the injection molding machine is not obvious. In practice, it is generally used in combination with fuzzy intelligent algorithm and genetic algorithm. In particular, BP neural network has strong nonlinear mapping ability and flexible network structure, which has good optimization effect on PID control algorithm, but it also has the defects of slow convergence speed and easy to fall into local minimum. For the design optimization of the hydraulic control system of the precision injection molding machine, the particle swarm optimization algorithm can be selected, combined with the BP neural network algorithm, and its high-precision PID parameters can be adjusted online. And fast convergence. After optimization design, the hydraulic control system of the injection molding machine mainly consists of PID controller, hydraulic oil pump of the injection molding machine, servo motor and pressure/flow sensor on the oil pump, forming a closed-loop system, which can meet the requirements of the whole system for high precision and rapid response.
There are two customized control modes for hydraulic system of injection molding machine
1、 Pressure control
As one of the important parameters that affect the performance and specifications of injection molding machines, pressure needs to provide corresponding hydraulic pressure for each action in the face of different injection molding processes. Therefore, attention should be paid to the analysis of pressure control state when designing the control system. Determine the fluid in the oil circuit
Pressure is the object of control. For the hydraulic system of constant displacement pump driven by AC servo motor, install a pressure transmitter in the main oil circuit to complete the detection of system hydraulic pressure. The pressure transmitter outputs 0-10V voltage signal. The CNC system of the injection molding machine needs to transmit the injection molding process pressure command processed by the servo controller to the servo motor starter. The pressure transmitter detects whether the hydraulic pressure reaches the set pressure value, and then the servo control adjusts the pressure control state. Then, compare the detected pressure value with the set pressure value, calculate and control the speed and torque of the servo motor, and drive the hydraulic pump to provide hydraulic pressure for the injection molding machine.
2、 Flow control
Flow control is to determine the flow of each action oil cylinder as the object, so as to ensure that each mechanism driven by the oil cylinder can act quickly to achieve a state of high production efficiency. Large injection molding machine After the numerical control system sends the flow command signal to the AC servo motor driver, it drives the AC servo motor to run and drives the quantitative hydraulic pump to run at a high speed. The volumetric efficiency of the constant displacement hydraulic pump is determined as a fixed value, and it is confirmed that the number of revolutions of the motor is linearly related to the hydraulic flow in the oil circuit, so that the purpose of controlling the hydraulic flow of the injection molding machine can be achieved by controlling the speed of the AC servo motor. Wherein, the relationship between the servo motor speed and the output flow of the constant displacement pump is: Q=CnV, Q represents the output flow of the constant displacement pump; N represents the speed of AC servo motor; C is the volumetric efficiency of the constant displacement pump; V is the rated displacement of oil pump.