The back pressure of the injection molding machine, also known as plasticizing pressure, is a force used to maintain the injection pressure. It is mainly because the pressure formed will push the screw back continuously when the molten material keeps entering the barrel. The back pressure is a reaction force against the screw back, which can slow down the screw back speed, so as to ensure that the molten material can be evenly injected into the barrel to make it full. Proper adjustment and use of back pressure can make the melt temperature even, compact the melt, and produce better plastic products. How to adjust injection molding machine Back pressure, what kind of back pressure is appropriate, Liansheng injection molding will answer for you one by one.
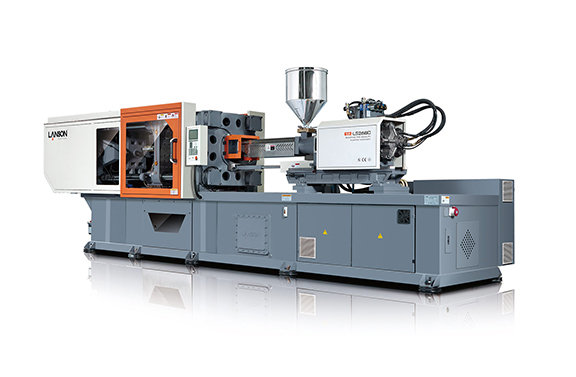
1、 Where is the back pressure calibration position?
The back pressure valve of the injection molding machine is generally next to the glue melting valve, and the back of the injection cylinder of the pre plasticizing screw injection molding machine is also equipped with a back pressure valve. The back pressure is controlled by adjusting the oil return throttle valve of the injection cylinder.
2、 How to determine the back pressure calibration value?
During the production of the injection molding machine, the back pressure adjustment value is not constant, usually 3-15kg/cm. The adjustment of back pressure is not only related to the nature of raw materials and the structural quality of products, but also needs to run through the whole production process. In case of glue leakage, salivation, excessive decomposition of molten materials, discoloration of products and slow return of materials at the nozzle during production, proper reduction of back pressure shall be considered. When it is found that there is a little air flaring, color mixing, shrinkage on the surface of the product, and the size and weight of the product change greatly, the back pressure should be appropriately increased. Therefore, the back pressure needs to be properly adjusted according to the production status and own production experience.
3、 Side effects caused by improper back pressure adjustment
If the back pressure is too low, the screw will recede rapidly, and the molten material will be mixed with more air into the barrel and become loose, resulting in poor plasticizing quality and unstable glue injection, which will lead to a large gap in size and weight of the product, air flaring, cold material lines on the surface of the product, bubbles in the interior, and dissatisfaction with glue flow around the product and at the bone position, It seriously affects product quality.
High back pressure will lead to slow screw retrogression, and low back pressure will lead to fast screw retrogression, affecting production efficiency. At the same time, the molten material pressure becomes higher, and the nozzle is prone to the phenomenon of sol salivation and glue leakage, leading to clogging of the nozzle or the formation of cold material spots, which is also a waste of raw materials. High back pressure will also cause excessive wear of the pre plastic mechanism and screw barrel machinery, reducing service life.
Proper back pressure is the driving factor to improve product quality, so mastering the adjustment of back pressure is conducive to improving production efficiency and quality.