In the process of injection molding, the generation of bubbles and defects is a problem that cannot be ignored in the quality of injection molded products. Large injection molding machine A series of measures have been taken to deal with bubbles and defects in the injection molding process to ensure the quality of injection molding products.
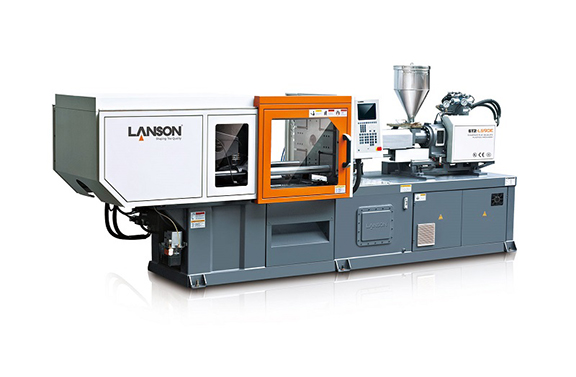
First of all, large injection molding machines need to process and dry plastic raw materials before injection molding. Humidity has an important impact on the melting and fluidity of plastic materials, and excessive humidity may lead to bubbles. Therefore, injection molding companies usually use special drying equipment to pretreat plastic raw materials to remove moisture and moisture and ensure that the drying degree of raw materials meets the requirements.
Secondly, large injection molding machines pay attention to mold design and adjustment in the injection process. Mold design plays an important role in the molding quality and appearance of injection products. Reasonable mold design can avoid bubbles and defects. At the same time, the injection molding machine operator needs to adjust the mold according to the actual situation to ensure that the plastic can fully fill the mold cavity and avoid cavity or uneven injection.
In addition, large injection molding machines need to control the injection speed and pressure during the injection molding process. Excessive injection speed and pressure may cause severe shear force during injection of plastic, which may cause bubbles and defects. Therefore, the injection molding machine operator needs to reasonably adjust the injection speed and pressure according to the requirements of injection molding products to ensure that the plastic can fill the mold cavity smoothly and reduce the generation of shear force.
In addition, large injection molding machines will also take some measures to eliminate bubbles and defects. For example, the injection molding machine is usually equipped with a vacuum pumping device to extract the air in the mold cavity during the injection molding process to reduce the generation of bubbles. At the same time, some injection molding machines are also equipped with a gas ejection device, which is used to exhaust the gas generated during the injection molding process from the mold cavity to reduce the formation of bubbles and defects.
Injection molding machine manufacturer To sum up, large injection molding machines deal with bubbles and defects in the injection process through multiple means such as plastic raw material processing and drying, mold design and adjustment, injection speed and pressure control, and bubble and defect elimination measures. The reasonable application and operation of these measures can improve the quality of injection molding products and meet the needs and requirements of customers. Injection molding companies need to pay full attention to and master these technologies to improve their competitiveness and product quality.