Preventive maintenance for injection molding machine Normal and stable operation in continuous production is very important. Both manufacturers and users of injection molding machines should be aware of the necessity of maintaining injection molding machines. The following sections will introduce how to ensure the normal and stable operation of the injection molding machine in continuous production.
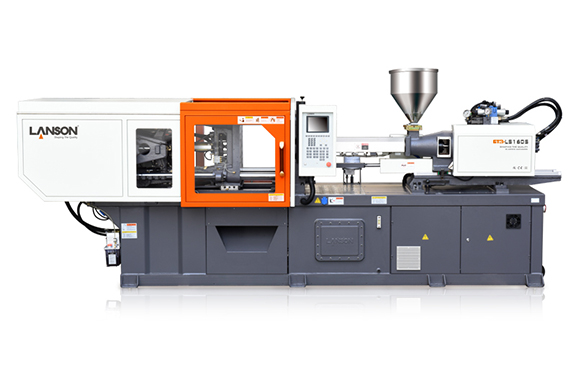
1. Hydraulic oil volume: ensuring sufficient hydraulic oil volume of the injection molding machine is the key to maintain its normal operation. Insufficient oil may lead to oil temperature rise and air entering the hydraulic system, thus affecting the oil quality and normal operation of the system. Oil leakage and loss during repair are one of the main reasons, so it is necessary to regularly check potential leakage points and replace worn seals in time.
2. Hydraulic oil temperature: the temperature of hydraulic oil is critical to the working performance of the injection molding machine. Maintaining the ideal operating temperature range of the hydraulic system from 45 ℃ to 50 ℃ can improve the control accuracy and response speed, and extend the life of the seals. Therefore, it is necessary to monitor the temperature of hydraulic oil to ensure that it is within the proper range.
3. Hydraulic oil quality: the quality of hydraulic oil is very important for the long-term stable operation of the injection molding machine. Oxidation is one of the main reasons for the aging of hydraulic oil. Oxidation will generate insoluble sediment, pollute the hydraulic system, and lead to wear and blockage. Therefore, the hydraulic oil needs to be replaced regularly to ensure its good quality.
4. Oil filter and cooler: oil filter and cooler are important parts of the hydraulic system and should be cleaned and maintained regularly. The cleaning of the oil filter can ensure that the oil is smooth and prevent blocking. The cleaning of the cooler can maintain the cooling efficiency and avoid overheating.
5. Regular maintenance: regular preventive maintenance is the key to ensure the normal operation of the injection molding machine. This includes inspection and replacement of worn seals, fastening of loose connections, cleaning of hydraulic components, etc. The maintenance work shall be carried out in accordance with the maintenance manual provided by the manufacturer and within the specified time.
6. Failure prediction and planned maintenance: failures of injection molding machines should be predicted and planned. Timely finding and replacing damaged parts can avoid chain failures and ensure the continuity of production.
Injection molding machine manufacturer In conclusion, preventive maintenance is the key to ensure the normal and stable operation of the injection molding machine in continuous production. Regular inspection, maintenance and reasonable oil management can extend the service life of the injection molding machine, improve production efficiency, reduce maintenance costs and ensure product quality. Both manufacturers and users should attach great importance to the maintenance work and incorporate it into the important link of production management.