Plastic injection molding machine It is a kind of commonly used manufacturing equipment, which is used to produce various plastic products, from daily necessities to industrial parts. Its workflow includes several key steps, and the following is linked Horizontal injection molding machine The editor will introduce these steps in detail to help understand the working principle of plastic injection molding.
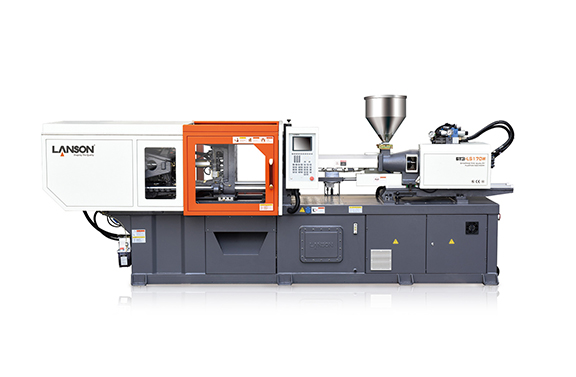
1. Feeding of plastic particles:
The first step of the workflow is to load plastic particles or granular raw materials into the feed hopper of the injection molding machine. These raw materials can be different types of plastic resins, such as polypropylene, polyethylene, polystyrene, etc. The specific selection depends on the requirements of the final product.
2. Heating and melting:
Once the raw materials enter the machine, they will be heated by a heating system, usually using electric heating elements or electromagnetic heating systems. When raw materials are heated to high enough temperature, they will melt into liquid state.
3. Ejection:
Molten plastic is pushed into the barrel of the injection cylinder through an injection cylinder. There is a screw rod inside the injection cylinder, which will send molten plastic into the mold chamber. This process is called injection. By controlling the movement of the screw rod, the precise injection quantity of each product can be controlled.
4. Pressure and cooling:
Once molten plastics enter the mold, they are subjected to high pressure to fill the mold cavity to form the desired shape. At the same time, the cooling system in the mold will start to work to quickly cool and solidify the plastic.
5. Mold opening:
Once the injection molding is completed, the mold is separated and the molded parts are released. This step usually takes some time to ensure that the finished product can be demoulded smoothly from the mold when the strength is sufficient.
6. Parts discharge:
After demoulding, the formed parts are discharged through a discharge system and moved to the next workstation or conveyor belt. The exhaust system usually consists of cylinders or mechanical arms.
7. Post treatment:
In some cases, formed parts may require post-treatment, such as trimming, grinding, assembly or painting. These jobs are usually completed on the workstation behind the injection molding machine.
8. Quality inspection:
After production, the finished products will be sent to the quality inspection department to ensure that they meet the specifications and quality standards. This includes inspection of dimensions, appearance, strength and other aspects.
9. Packaging and shipment:
The parts passing the quality inspection will be packed and ready for shipment. Packaging is usually customized according to the nature and purpose of the product to ensure safety and protection.
The above are the main workflow steps of the plastic injection molding machine. This process requires a high degree of automation and precise control to ensure that each product meets the specifications and has consistent quality. The plastic injection molding machine is widely used in automobile manufacturing, electronic manufacturing, medical equipment manufacturing and consumer goods production, so it is very important to precisely control the workflow.