What problems will occur during the transformation of the inverter of the injection molding machine? With the popularization of frequency control technology, frequency control technology has been widely used in the field of drive control and energy saving, especially in injection molding machine Under the condition of (pump) load, the energy-saving effect of frequency conversion control is remarkable. However, when we install, debug and use the inverter on the injection molding machine, we often encounter some troublesome problems. How to ensure the normal operation of the inverter and reduce the failure rate of the inverter has become a problem that our technicians need to face.
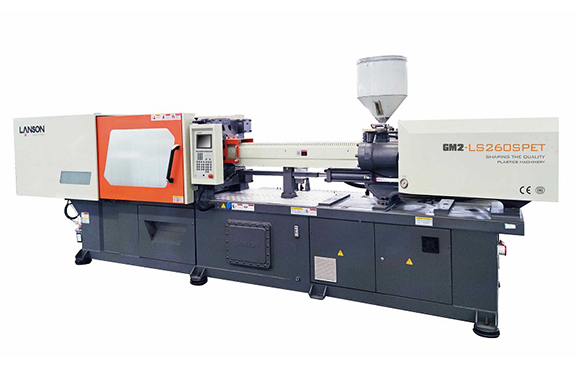
In a cycle of injection molding: mold closing - injection molding - pressure maintaining - feeding - cooling - mold opening - ejector pin - discharging, the requirements for flow and pressure are different. Generally, the injection and mold closing stages are different. The demand for flow and pressure is large, but the demand for flow and pressure is small in the cooling and recovery stages. Before the frequency conversion of the injection molding machine, the displacement of the oil pump in each working cycle is basically unchanged. When the load becomes smaller, the actual flow required is very small, and the excess flow overflows through the overflow valve, resulting in huge energy loss.
High speed injection molding machine After the transformation of frequency conversion for energy saving, by collecting the proportional pressure and proportional flow signals of the NC system of the injection molding machine, the motor running speed corresponding to each action of the frequency converter is automatically adjusted, so that the flow and pressure output by the oil pump can just meet the working needs of the molding machine system; In the non action state (mainly cooling state), let the motor run at a low speed, so as to greatly reduce the energy consumption of the injection molding machine, and then achieve the purpose of energy saving.